Impresión 3D para la industria de la joyería: todo lo que necesitas saber
Según un informe publicado en 2017 por la multinacional financiera y aseguradora ING, en tan sólo un par de décadas la mitad de los productos que consumimos podrían ser fruto de la aplicación de esta tecnología en los procesos productivos de industrias muy diversas.
Con total seguridad la industria de la joyería se encontrará entre ellas.
La manufactura de joyas, como actividad económica, se remonta a los albores de la humanidad.
El artífice joyero ha sido testigo y protagonista de las sucesivas innovaciones tecnológicas que se han ido sucediendo siglo tras siglo, pero todo apunta a que en la larga historia de la joyería ningún avance técnico ha tenido el impacto que ya está teniendo la fabricación aditiva y por eso he querido prestarle especial atención desde el primer momento.
Este repositorio de información acerca de los efectos producidos por la generalización del uso del diseño asistido por ordenador y de la impresión 3D en la industria joyera tiene un objetivo claro: ayudarte a comprender los efectos de la impresión 3D en la fabricación de joyas, siempre desde la perspectiva de la gestión empresarial.
Este repositorio de información acerca de los efectos producidos por la generalización del uso del diseño asistido por ordenador y de la impresión 3D en la industria joyera tiene un objetivo claro: ayudarte a comprender los efectos de la impresión 3D en la fabricación de joyas, siempre desde la perspectiva de la gestión empresarial.

Ventajas de la impresión 3D
Comencemos por el principio.
Comencemos por el principio.
Antes de la generalización de la impresión 3D el primer paso para que un diseño en formato digital se trasladase a un equipo para ser reproducido de forma autónoma, ya fuese en metal (como un grabado) o en cera para microfusión, fue la combinación de diseño asistido por ordenador (CAD-CAM) con máquinas de control numérico (CNC).
La impresión 3D nos ha permitido superar muchas de las limitaciones del CNC, puesto que no depende de la cantidad de ejes disponibles, es más rápida y su funcionamiento es más sencillo.

El diseño CAD-CAM se caracteriza por:
Posibilitar el desarrollo de diseños inviables por otros medios.
Garantizar precisión absoluta.
Simplificar la introducción de modificaciones en un diseño, haciendo el desarrollo de variantes rápido y fácil (introducir nuevos elementos o suprimir alguno de los existentes, redimensionar o incluso regresar a una versión previa es sencillo).
Posibilitar el desarrollo de diseños inviables por otros medios.
Garantizar precisión absoluta.
Simplificar la introducción de modificaciones en un diseño, haciendo el desarrollo de variantes rápido y fácil (introducir nuevos elementos o suprimir alguno de los existentes, redimensionar o incluso regresar a una versión previa es sencillo).
Como cualquier producto digital, un diseño en formato digital es susceptible de ser almacenado y compartido de forma inmediata y segura con un coste ínfimo.
Minimizar la necesidad de incurrir en costes de producción, ya que la disponibilidad de imágenes digitales fotorrealistas creadas a partir de un modelo 3D (render) permiten la elaboración de portafolios de producto en formato digital.

¿Cuáles son las principales ventajas de la impresión 3D para joyería?
Pone a tu alcance la posibilidad de materializar diseños que sería imposible ejecutar de ninguna otra forma.
Te asegura la replicabilidad de un diseño, ya que la precisión y la fiabilidad de estos sistemas es total:
A- Son garantía de perfección.
B- Simplifica la fabricación de ciertos diseños (por ejemplo, minimizando la necesidad de soldar).
C- Libera tiempo para la ejecución de otras tareas, mejorando tu eficiencia en el proceso de producción.
D- Acelera tu proceso de producción (por ejemplo, permitiendo la impresión de piezas en lotes).
E- Gracias a que convierte el prototipado en un juego de niños, te permite examinar un diseño de forma sencilla y barata antes de su fabricación.

Ahora bien, la impresión 3D presenta ciertos retos que debes tomar en consideración: tendrás que formarte en modelado 3D y en la utilización del dispositivo de impresión 3D que escojas, necesitarás familiarizarte con las particularidades del proceso de microfusión con el material de impresión correspondiente, todo esto requiere recursos, dinero, tiempo, esfuerzo.
¿Qué debes sopesar a la hora de seleccionar una impresora 3D para la fabricación de joyas?

El ecosistema de la fabricación aditiva está más vivo que nunca.
Las innovaciones se suceden a una velocidad pasmosa y nuevos jugadores entran en el terreno de juego con propuestas de lo más diversas.
Por consiguiente, elegir un equipo de impresión 3D para joyería puede llegar a ser una tarea titánica.
¿Qué variables has de considerar?
A continuación encontrarás las más destacables, tanto desde el punto de vista técnico como desde el económico:
1- Aptitud para la fabricación de joyas.-
¿El equipo cumple los requisitos mínimos para el uso previsto?
Presta atención a parámetros como su resolución, las dimensiones de su área de trabajo, los materiales de impresión o su facilidad de uso.
2- Servicio post-venta.-
¿Vas a tener acceso a un servicio de asistencia técnica fiable?
Todos los equipos necesitan mantenimiento y, como es evidente, el soporte juega un papel clave cuando surgen dificultades.
3- Retorno de la inversión.-
La adquisición de un equipo de impresión 3D no deja de ser una inversión y, por consiguiente, debes tener la certeza de que va a ser rentabilizable.
En función del desembolso económico a realizar, tendrás que calcular el plazo de amortización de este inmovilizado material atendiendo a unos patrones de uso concretos, considerando mantenimiento y consumibles.
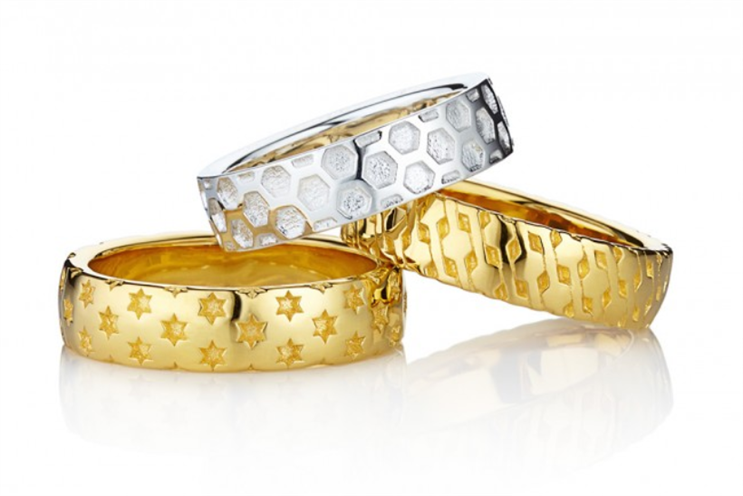
¿No prevés un uso intensivo del equipo? Entonces lo más probable es que subcontratar los servicios de impresión sea la opción más inteligente para ti.
Principales tecnologías de impresión 3DA continuación encontrarás una selección de artículos que resumen las principales características de las tecnologías de fabricación aditiva más extendidas:
* Estereolitografía
* Modelado por deposición fundida – FDM
* Polyjet
* Sinterizado selectivo por láser – SLS
Tanto la estereolitografía como el modelado por deposición fundida son tecnologías que se emplean de forma habitual para la impresión de prototipos de diseños en materiales termofusibles, que se utilizan en la fabricación de piezas de joyería mediante la técnica de la microfusión (fundición a la cera perdida).
Conoce cuáles son las diferencias entres las impresoras cartesianas, polares, deltas y los brazos robóticos.
Impresoras 3D cartesianas
Es sin dudarlo el tipo de impresora FDM más común que hay en el mercado, reciben este nombre debido a que utilizan un sistema de coordenadas dimensionales -el eje X, Y y Z- que se utiliza para determinar dónde y cómo moverse en tres dimensiones, estos son utilizados para determinar la correcta localización del cabezal de impresión y corregir la dirección del movimiento.
La cama de impresión de esta máquinas se mueve únicamente en el eje Z, el extrusor se sitúa sobre el eje X y el Y, así puede moverse en cuatro direcciones. En esta categoría encontramos algunas de las marcas más conocidas de la industria como Ultimaker o Makerbot.
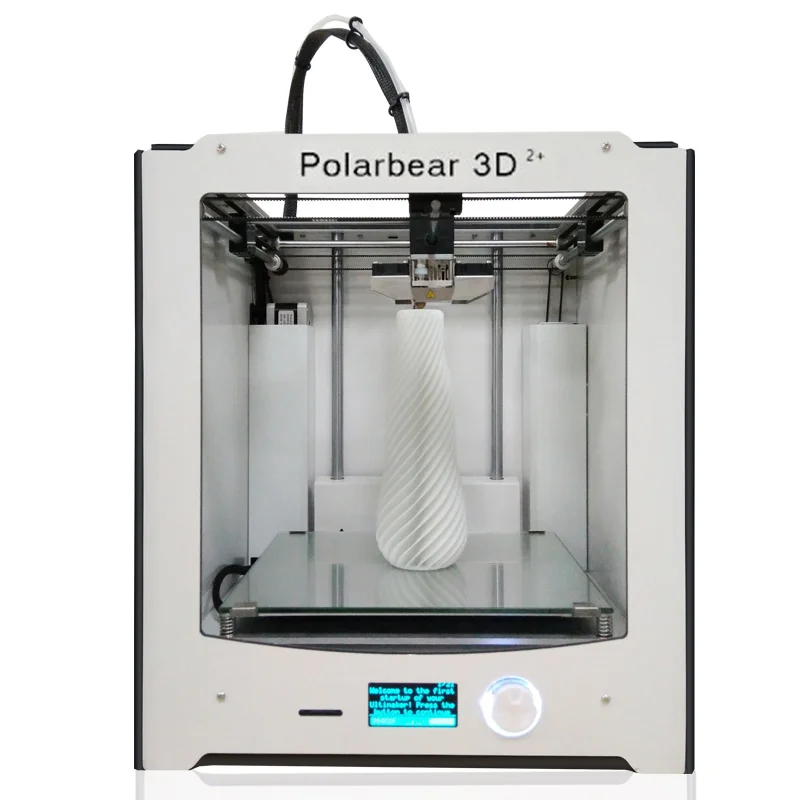
Impresoras 3D Polares
La diferencia entre esta máquina con respecto a las cartesianas, es que está utiliza las coordenadas polares para imprimir en 3D. Los conjuntos de coordenadas describen puntos en una cuadrícula circular en lugar de un cuadrado, no determinados por los ejes X,Y y Z, pero con ángulo y longitud.Esto significa que la cama de impresión gira, y la cabeza de impresión puede moverse hacia arriba, abajo, izquierda y derecha; y el extrusor puede moverse de arriba a abajo.
Una ventaja a destacar de estos tipos de impresoras 3D es que pueden funcionar solo con dos motores, y una impresora cartesiana requiere un motor por cada eje, al menos tres, lo que supone un ahorro a largo plazo. Otro punto a favor es que la impresora puede tener un mayor volumen de construcción dentro de un espacio más pequeño.
Impresora 3D Delta
El estilo de la impresora 3D Delta está ganando gran popularidad últimamente. Ya te presentamos a los estudiantes suizos que crearon una impresora de seis ejes, basada en la técnica delta. Trabajan con coordenadas cartesianas y sus características principales son la cama de impresión circular combinada con el extrusor que se fija por encima con una configuración triangular, a esto se le atribuye el nombre “Delta”. Cada uno de los 3 dispositivos puede moverse hacia arriba y hacia abajo, lo que permite que el cabezal de impresión se mueva en tres dimensiones.
Las impresoras 3D Delta fueron diseñadas para aumentar la velocidad de impresión, y con una cama de impresión sin movimiento, lo que puede resultar útil para ciertos proyectos. Sin embargo, a veces se argumenta que esta categoría de impresoras no es tan precisa como las cartesianas.

Brazos robóticos
Actualmente hay muchos brazos robóticos utilizados para la operación industrial en una línea de montaje de automóviles, pero su función principal es el montaje de piezas de automóviles y no de filamentos de extrusión. La impresión con un brazo robótico está todavía en desarrollo, en pocas compañías. Es principalmente el negocio de la construcción el que lo utiliza.
Sin embargo, este método de impresión FDM 3D está surgiendo, ya que no necesita una cama de impresión fija y tiene una mayor movilidad. El movimiento de la cabeza del extrusor es también extremadamente flexible, abriendo un montón de nuevas posibilidades de diseños complejos. Desafortunadamente, la calidad todavía no está tan cerca de una impresora cartesiana, muchas compañías están trabajando en su desarrollo.
FDM o modelado por deposición fundida.
Esta tecnología, más conocida como FDM de las siglas en inglés Fused Deposition Modeling (también FFF Fused Filament Fabrication, fue desarrollada por S. Scott Crump a finales de 1980 y comercializada en 1990 por Stratasys (EE.UU.. Otro año clave para esta tecnología es 2005, cuando el profesor Adrian Browyer inició el proyecto RepRap, el movimiento mundial detrás de la auto-replicación de impresoras 3D de código abierto.
Funcionamiento de la impresión 3D por deposición fundida
Esta técnica es considerada a menudo el método existente más sencillo. La tecnología de modelado por deposición fundida o FDM se basa en 3 elementos principales: una placa/cama de impresión en la que se imprime la pieza, una bobina de filamento que sirve como material de impresión y una cabeza de extrusión también llamada extrusor. En resumen, el filamento es succionado y fundido por el extrusor de la impresora 3D, que deposita el material de forma precisa capa por capa sobre la cama de impresión.
Quien dice “impresión 3D” dice “modelo 3D”: todo comienza con el diseño del objeto utilizando algún software CAD (como SolidWorks, TinkerCAD o Blender, por ejemplo). El archivo 3D resultante, en su mayoría en formato .STL, se divide en varias capas utilizando un software denominado “slicer” (como Makerware, Cura o Repetier) en el que es posible seleccionar los distintos parámetros de a impresión. Una vez configurado todo, se puede iniciar la impresión.
La impresión 3D comienza cuando la maquina alcanza una temperatura alrededor de los 200°C, necesaria para la fusión del material. Entre los materiales de impresión 3D más populares en la deposición por fusión se encuentran el PLA (ácido poliacético) y el ABS (Acrilonitrilo butadieno estireno).
Una vez que se calienta la máquina, se extruye un filamento de material de 1,75 mm o 2,85 mm de diámetro sobre la plataforma a través de una boquilla que se mueve sobre 3 ejes x, y y z. La plataforma desciende un nivel con cada nueva capa aplicada, hasta que se imprima el objeto.
Durante la impresión, se pueden utilizar soportes para mejorar la calidad de ciertos modelos. Su función es apoyar las partes sobresalientes del modelo 3D, ya que hay ciertos modelos que sin apoyo es muy difícil que consigan ser impresos. Estos soportes pueden estar hechos del mismo material que el objeto impreso o en un material que sea soluble en agua o limoneno por ejemplo. Aunque es más complicado de manejar, algunas impresoras 3D están equipadas con varios extrusores para combinar varios colores o materiales (materiales de soporte en general).
Materiales compatibles con el modelado por deposición fundida
La impresión 3D de depisición fundida es compatible con una amplia variedad de polímeros termoplásticos: PLA y ABS, y también de policarbonato como, PET, PS, ASA, PVA, nylon, ULTEM y muchos filamentos compuestos que estén basados en metal, piedra, madera. Esto ofrece interesantes propiedades mecánicas tales como conductividad, biocompatibilidad, resistencia a temperaturas o condiciones extremas, por mencionar algunos. Al reemplazar el extrusor de la impresora 3D con un sistema de jeringa, también es posible crear piezas de cerámica, arcilla o materiales alimenticios (como jarabe o chocolate). Para dar una idea del precio de los consumibles para impresoras 3D, un carrete de 1kg de filamento PLA es de unos 35 €.
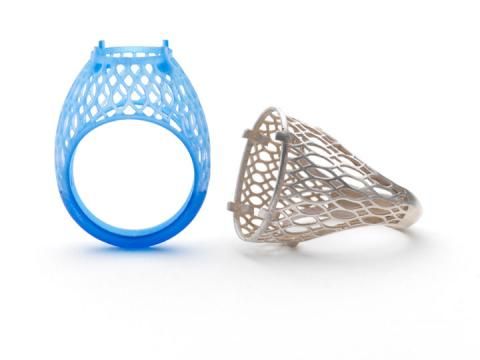
Nuevos proyectos también han surgido con el deseo de ofrecer piezas policromadas que combinan miles de colores. La Da Vinci Color del fabricante XYZprinting, RoVa4D de Ord Solutions o la Palette+ de Mosaic Manufacturing , estas pueden combinar los filamentos de color con el fin de obtener toda la gama de colores CMYK (Cian, Magenta, Amarillo y Negro), y llegar a más de 10 millones de combinaciones de colores disponibles. Sin embargo, estas iniciativas siguen siendo relativamente nuevas.
Precio, rendimiento y especificaciones de la impresión 3D FDM
En el modelado por deposición fundida, las impresoras 3D tienen un rango de precio a partir de 300€ para los primeros modelos de impresoras 3D que puedes montar por ti mismo (tipo RepRap), 2.500 € para los modelos de gama media y cerca de 10.000 € para las máquinas de FDM profesionales. Entre los actores más destacados están el fabricante histórico Stratasys, pero también marcas del movimiento de RepRap tales como MakerBot (adquirido por Stratasys en 2013), Ultimaker o Prusa. Encontrarás más de las marcas destacadas dentro de nuestro comparador.
Aunque algunas impresoras 3D tienen un espesor de capa de impresión de hasta 50 micras, los resultados de postprocesado son todavía menos buenos en comparación con otras tecnologías tales como estereolitografía o la sinterización por láser. Con respecto al volumen máximo de fabricación, las impresoras 3D generalmente permiten alcanzar un volumen de entre 12x12x12 cm y 30x30x30 cm para las más voluminosos. Las impresoras 3D FDM XXL, que superan el metro cúbico, también se han dado a conocer y aquí destacan nombre como BigRep One o 3DP WorkBench de la American 3DPlatform.

Con la tecnología de modelado por deposición fundida es fácil apreciar las capas de impresión, como el el modelo de 3D Benchy
También hay diferentes categorías de impresoras de modelado por deposición fundida dependiendo del mecanismo utilizado. Las impresoras cartesianas 3D usan coordenadas en los 3 planos (X, Y y Z) como sugiere su nombre, mientras que los modelos polares usan coordenadas polares (ángulo y longitud). Las impresoras Delta 3D también están disponibles, con una estructura vertical, una bandeja de impresión redonda y un extrusor fijo de tres brazos. Más recientemente surgieron en el mercado de la impresión 3D los brazos robóticos con múltiples ejes de rotación.
Su coste, su manejo o su velocidad de ejecución hacen que la tecnología de deposición de material fundido sea una técnica utilizada en muchos campos: aeroespacial, automótriz, arquitectura, medicina, decoración, arte y hasta cocina, principalmente para aplicaciones de tipo de prototipado rápido o validación de modelos visuales y/o partes funcionales. Con su gran catálogo de termoplásticos, la extrusión de filamentos también se puede utilizar para la producción en serie a nivel básico.
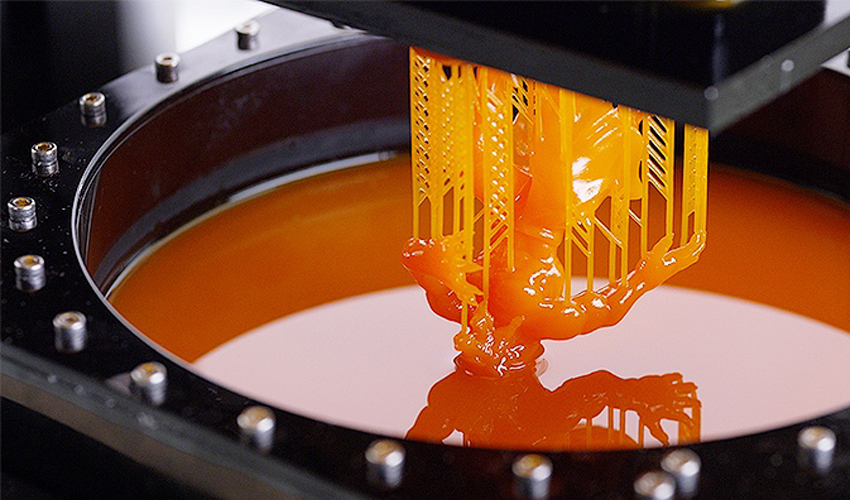
Impresión 3D por estereolitografía.
La estereolitografía se considera como el origen de los procesos de impresión 3D, con el primer equipo patentado en 1984 por Charles Hull y la primera máquina comercial desarrollada por 3D Systems en 1988. ¿ Qué hay detrás de esta técnica ?
Este proceso, conocido como SLA (estereolitografía), utiliza el principio de fotopolimerización para crear modelos 3D a partir de resinas sensible a los rayos UV. Esto se solidifica mediante el paso de un láser capa por capa, dotando con esto de mayor calidad a los modelos hechos con esta tecnologías.
Desde un punto de vista histórico, la estereolitografía se considera como el proceso detrás de la impresión 3D, algunos días antes del estadounidense, un trío de investigadores franceses compuesto por Jean-Claude André, Olivier de Witte y Alain le Méhauté imaginaron una patente similar en nombre del grupo Alcatel, una patente que desde entonces ha caído en desuso.
Las impresoras 3D SLA se caracterizan por su material de impresión líquido y por la presencia de una cubierta de protección UV (generalmente naranja, verde, rojo o amarillo). Ofrecen un volumen de producción relativamente pequeño en comparación con otras tecnologías de impresión, incluso algunas máquinas como la Mammoth de Materialise pueden producir piezas de más de 2 metros.
¿Cómo funciona la impresión 3D por estereolitografía?
Al igual que con cualquier técnica de impresión 3D, se requiere un archivo digital en 3D. Esto se puede obtener a través del software CAD (SolidWorks, Sculpt o Maya, por ejemplo). Este archivo, a menudo en formato STL, se envía a la máquina, donde un segundo software (llamado slicer) realiza un corte del modelo en capas delgadas de impresión de un espesor fijo. Y finalmente se le da la orden a la impresora de comenzar a imprimir.
Entre los diversos componentes de una máquina de estereolitografía se encuentran una bandeja de resina, una plataforma móvil (eje Z), un sistema de raspado (eje X), un láser UV, óptica de enfoque y un espejo galvanométrico (ejes X e Y).
El rayo láser barre la superficie de la resina líquida de acuerdo con el modelo 3D digital suministrado a la impresora. Una vez que la primera capa de material solidificado, la plataforma desciende un nivel, que corresponde al grosor de una capa de impresión, y una nueva sección se solidifica. Hay tantos ciclos de impresión como capas hay para obtener el volumen completo de la pieza.
En algunos modelos de máquinas SLA (como en Formlabs, por ejemplo), la producción de la pieza se realiza en reversa. La plataforma se sumerge en la bandeja de resina después de cada capa solidificada mientras que el láser actúa de abajo hacia arriba.

La tecnología SLA utiliza un material en forma de resina líquida fotosensible
Después de terminar la impresión, pasamos a la etapa de limpieza con un disolvente (generalmente alcohol isopropílico también conocido como isopropanol), esto es necesario para eliminar el exceso de resina no solidificada. A diferencia de otras técnicas tales como la sinterización selectiva por láser (SLS), la Deposición de Material Fundido (FDM) y la impresión PolyJet 3D, se requiere un post-procesamiento para finalizar el proceso de fotopolimerización y conseguir la maximiza fuerza del material.
Al igual que con la tecnología FDM, la estereolitografía utiliza el uso de soportes al imprimir formas complejas. En forma de andamios, que permiten soportar las partes que se precipitan en el vacío. Estos soportes son eliminados con facilidad durante el postproceso de los modelos.
La tecnología de estereolitografía ofrece un acabado superficial ligeramente vítreo, pero generalmente es superior a los procesos FDM o SLS (con el mismo espesor de capa). No es raro que las diferentes capas de impresión sean apenas visibles. Sin embargo, pocos colores están disponibles en SLA.
La tecnología 3D SLA ha generado muchas tecnologías
Tras la caída de las primeras patentes relacionadas con estereolitografía, muchos actores han trabajado para mejorar la tecnología. El método DLP, que utiliza un proyector de video en lugar del láser para cubrir un área más amplia, con una mayor velocidad de impresión, es un ejemplo de ello. La empresa francesa Prodways también ha desarrollado una técnica llamada MovingLight que mueve un video proyector, para acelerar aún más la producción de partes. La empresa británica Photocentric utiliza una pantalla LCD como fuente de luz ultravioleta.

Más recientemente, el fabricante estadounidense Carbon3D dio a conocer su método CLIP ( Liquid Interface, para la producción continua) que viene muy finamente controlar la cantidad de oxígeno durante la reacción de fotopolimerización, con la llave, una velocidad de impresión 25 a 100 veces más rápida. Otra iniciativa interesante relacionada con estas tecnologías es ONO, que recaudó $ 2.3 millones para un sistema que usa la luz de un teléfono inteligente para solidificar la resina.
Entre los principales fabricantes de impresoras 3D SLA, evidentemente se encuentra 3D Systems, iniciador de la tecnología. Jugadores más recientes también han comenzado a unirse a los desarrollos como DWSlab, B9Creator o Formlabs. Este último, con sede en Boston, puso en marcha en 2011 una campaña de crowdfunding en Kickstarter, consiguiendo la friolera de $ 3 millones, lo cual les permitio producir la Forma 1, la primera impresora SLA de escritorio, comercializada a $ 5.000.
El precio de las impresoras 3D por estereolitografía varía desde 1.000 € para las versiones de bajo costo hasta varias decenas de miles de euros para las máquinas profesionales con un gran volumen de fabricación. Puedes encontrar aquí nuestra selección con las mejores impresora 3D de resina.

Aplicaciones de la estereolitografía
La tecnología SLA es la más utilizada para la creación de prototipos, en todas las áreas de la industria gracias a su velocidad, pero dependiendo de la calidad de la impresora, también es posible obtener piezas funcionales inmediatas. SLA también se utiliza para la producción de moldes de inyección o fundiciones, especialmente en el mundo de la joyería y la odontología.
La fundición a la cera perdida es un ejemplo de un proceso de fabricación indirecto que utiliza estereolitografía. Esta técnica milenaria ahora descansa en la impresión 3D de una réplica fiel del modelo final (también llamado maestro de joyería) en una cera calcinable. Una vez que se imprime la forma, se envuelve en un material refractario, creando el molde. Luego se vierte un metal fundido en el molde y viene a reemplazar la cera. Una vez despejado del molde, la parte metálica estará disponible.
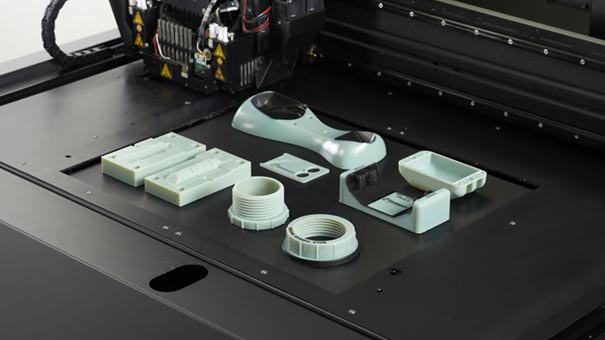
La impresión 3D PolyJet.
La impresión 3D PolyJet, patentada por la sociedad Objet Ltd. en 1999 (que se fusionó con Stratasys en 2012), combina la tecnología Inkjet y el uso de foto-polímeros – dos materiales se solidifican al contacto con la luz ultravioleta. Esta tecnología presenta varias ventajas : una excelente resolución – hasta 0.016 mm -, superficies lisas – sin efectos de escalera como en el caso de los objetos impresos por FDM – y una amplia gama de materiales y colores con un costo y un tiempo de impresión relativamente bajos.
Como toda técnica de impresión 3D, el proceso comienza con el modelado del objeto deseado utilizando un software de CAD (AutoCAD, Inventor o SolidEdge por ejemplo). Luego, el archivo 3D asociado es enviado a la impresora y el software de la impresora divide el modelo 3D en una multitud de imágenes numéricas, cada una correspondiente a una capa del objeto.
Las cabezas de impresión poseen cada una varias decenas de boquillas que proyectan micro-gotas de materia sobre una plataforma. Durante cada proyección, una luz ultravioleta es emitida y solidifica la materia.
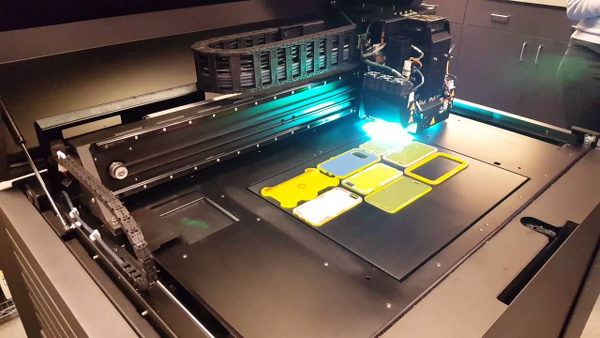
Estas etapas son repetidas, capa por capa, hasta la obtención de la pieza, la cual no necesita ninguna etapa de terminación (cocido, lijado, pulido). Para las geometrías complejas, un material de soporte (un gel fácil a retirar a la mano o con agua) es ajustado por una de las cabezas de impresión.
La impresión 3D Polyjet es compatible con una amplia gama de materiales (mas de 120 aproximadamente) y permite incluso de combinar varios simultáneamente (cada uno almacenado en una cabeza de impresión distinta). El material compuesto obtenido, Material Digital, permite obtener prototipos de alto desempeño para asemejarse al modelo final (resistencia a la temperatura, biocompatibilidad, rigidez, flexibilidad) y en variedad de colores.
En consecuencia, esta técnica es utilizada en distintas áreas: arquitectura, medicina, en la fabricación de juguetes, en la industria aeroespacial, pero también en las artes creativas.
La sociedad Stratasys comercializa 3 máquinas que utilizan esta tecnología de impresión 3D: Objet Desktop, Eden y Connex.
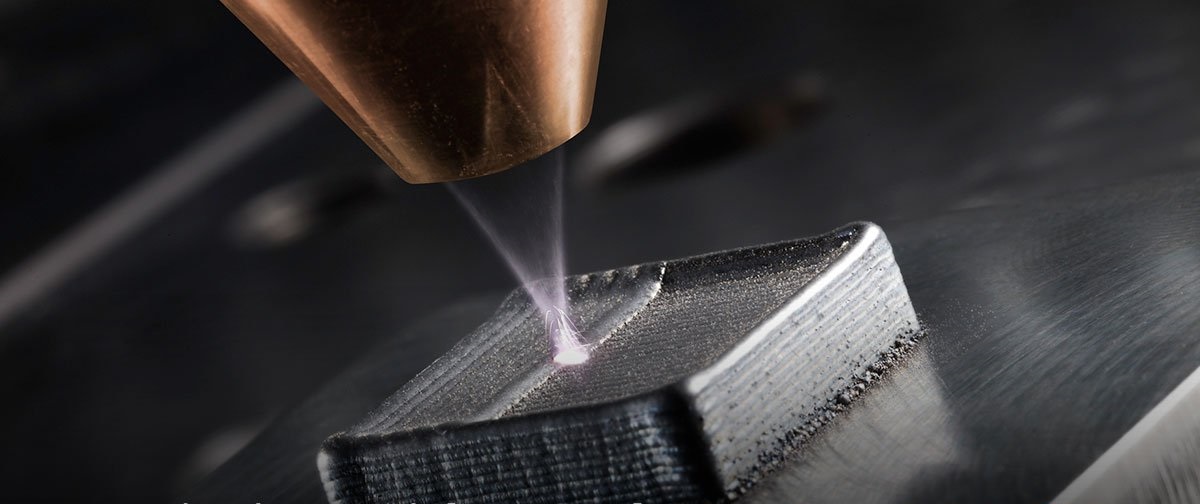
Sinterizado selectivo por láser.
El sinterizado selectivo por láser, conocido en inglés bajo el nombre de SLS (selective laser sintering), permite imprimir objetos funcionales sin recurrir a un aglutinante intermediario o a una eventual etapa de ensamble. Antes de la impresión, la concepción del objeto es realizada a partir de un software de CAD (CATIA, SolidWorks, ProEngineer por ejemplo) para que este sea enviado a una impresora en formato numérico. Luego, la impresión se realiza capa por capa, a partir de polvos fusionados, gracias a la temperatura generada por un láser CO2.
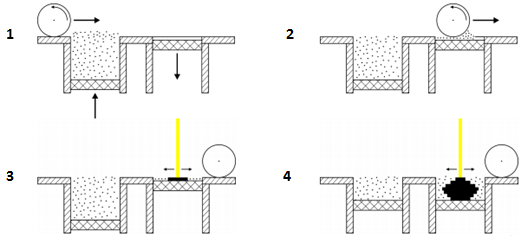
Inicialmente, se llena un primer recipiente de material en polvo mientras que un segundo recipiente sigue vacío. Cada recipiente tienen un pistón, ubicado en la parte inferior en el caso del recipiente lleno y en la parte superior – al nivel de la superficie de la mesa – para el recipiente vacío. El proceso comienza con el depósito de una capa fina de polvo (del orden de 0.1 mm). A cada ida y vuelta, el primer pistón se eleva mientras que el segundo pistón baja de una ranura equivalente al espesor de la capa (1). En la segunda etapa, un rodillo pasa sobre el polvo y deposita una fina capa sobre el segundo recipiente (2). La capa depositada es recorrida por el rayo láser que provoca la fusión y la consolidación del polvo (3). Las etapas son repetidas hasta obtener la pieza sólida en 3D correspondiente al archivo CAD de origen (4).
Esta tecnología hace posible la fabricación de objetos a partir de una amplia gama de materiales – como metales (titanio, acero y aleaciones) y los polímeros – respetando las altas exigencias de las piezas funcionales, como la resistencia mecánica y la resistencia química a la temperatura. Ademas, este procedimiento permite obtener piezas coloreables y sin límites de forma gracias a la ausencia de soportes, logrando al mismo tiempo, un alto nivel de calidad del producto y una gran estabilidad a lo largo del proceso de fabricación.
En consecuencia, este proceso es utilizado, no solamente en el área de diseño sino también en la industria automóvil, la aeronáutica y en la ingeniería biomédica (las piezas impresas son biocompatibles). Los dos grandes fabricantes de impresoras que utilizan el sinterizado selectivo por láser son 3D Systems y EOS GmbH, cada cual proponiendo una extensa lista de impresoras.
Dato curioso: Un proceso similar fue inventado por R.F Housholder quien patentó el concepto desde 1979, pero que nunca fue comercializado.

Impresión 3D de metal
Parece claro que si hay una tecnología de fabricación aditiva que va a contar con una importancia extraordinaria para el sector joyero será aquella que permita construir objetos metálicos, como es el sinterizado selectivo por láser.
Parece claro que si hay una tecnología de fabricación aditiva que va a contar con una importancia extraordinaria para el sector joyero será aquella que permita construir objetos metálicos, como es el sinterizado selectivo por láser.
Impresoras 3D en metal que ya son una realidad para la industria de la joyería.
El presente es importante, pero merece la pena que también le dediquemos atención al alcance futuro de esta tecnología en el sector joyero.
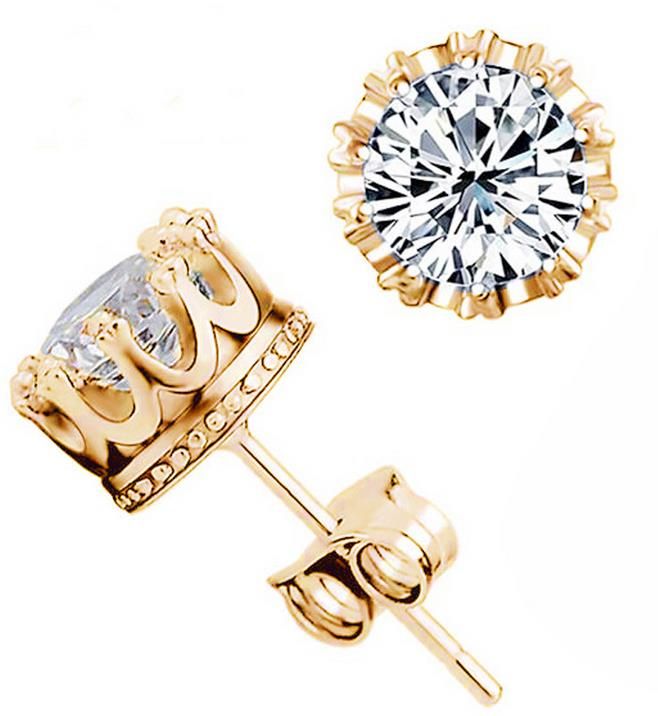
Fernando Gatto
Kaia Joyas Uruguay
No hay comentarios.:
Publicar un comentario